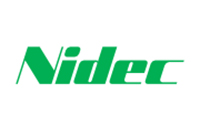
Let us reintroduce ourselves – experienced company with a new name
We are Nidec Machine Tool America, formerly part of Mitsubishi. Our machine tool heritage began in 1936, and continues with renewed dedication. For you, as a gear maker, we supply and support hobbers, shapers, shavers, skiving machines, and internal and external generating gear grinders. We do cutting tools, too.
Read More | 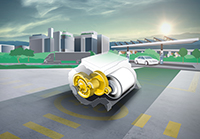
Gear solutions for e-mobility by Liebherr
New drive technologies in electric mobility are changing the requirements for gears and therefore for the quality of the tooth flank surfaces. Liebherr has addressed this issue and refined various technological solutions for e-gearboxes. Generating grinding with dressing-free CBN grinding worms, for example, ensures a high degree of process reliability.
Read More | 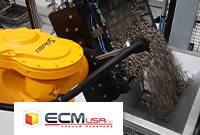
Advanced Automation for Heat Treat Production Lines
ECM ADVANCED AUTOMATION is the ideal solution for integrating & managing leading-edge robotic technology for your production line. Automate an existing or new heat treat system to assure a more reliable process from part sorting & load building to transport using AGVs in an ECM vacuum furnace or peripheral equipment. www.ecm-usa.com
Read More |
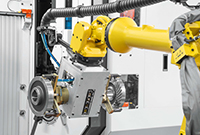
Precision Automation for Large Parts Handling
New Gleason Automation for load/unload of larger parts speeds throughput, optimizes the process flow – and lifts the burden off the machine operator. The AR Series uses advanced vision guidance to ID the part and ensure proper orientation before loading it into the machine, even if it arrives without precise location directly from dunnage. Easily integrated with pre-and post-processes such as part washing, deburring, inspection and marking.
See It In Action | 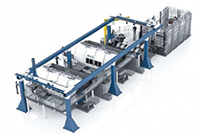
WFL Examines Evolution of Automation
The ever-greater variety of models has meant that transfer lines have tended to be replaced by flexible line chains or by individual cells with a variable material flow. Using intelligent software in combination with the relevant automation solutions not only enables workpieces to be loaded and unloaded but also means that machining centres can be set up fully automatically through the automatic replacement of tools and clamping devices.
Read More | 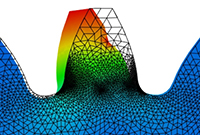
KISSsoft Includes FEM Calculations
FEM calculations have been included in KISSsoft on a long-term basis. For the calculation of planet carriers, gear body deflections and gear root stresses, FEM is used in order to better take into account complex geometric and/or loading conditions.
Read More |