 |
|
 |
Chamfering Can Make the Difference—The Choice Is Yours |
They say necessity is the mother of invention. The arrival of a new generation of cylindrical gear chamfering solutions in recent years isn’t by accident. Gear manufacturers who might have turned a deaf ear to a new chamfering technology just a few years ago now welcome it with open arms. After all, the benefits of quality chamfering are now well-known, and their application is near-mandatory. Inadequate and uneven chamfers cause extraordinary costs when applying expensive hard-finishing tools down the value stream. Gears that aren’t properly chamfered and deburred can lead to overloaded edges and unanticipated and undesirable noise.
|
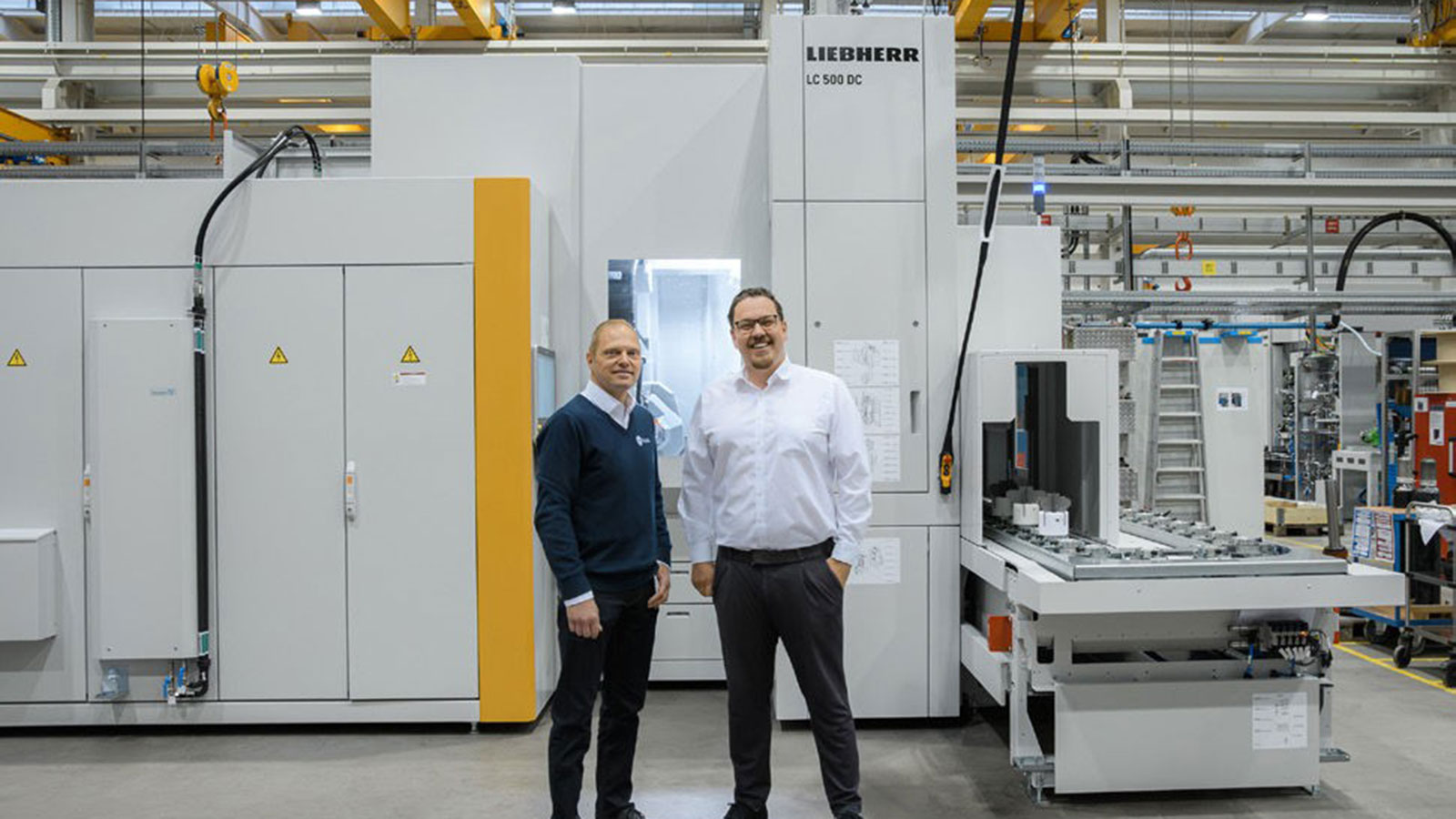 |
Machine and Tool Concepts for Contract Manufacturing |
Due to increased order volume for a large agricultural machinery manufacturer, an LC 500 DC was added to SPN’s machinery in April 2024. The decisive factor in their decision to purchase it was the integrated machining unit, which combines two chamfering technologies in one machine—a special feature of the new generation of machines. In addition to the fast, economical ChamferCut process, FlexChamfering—chamfering with common end mills—is particularly attractive for SPN, as it is suitable for small batch sizes. The flexible LC 500 DC enables a wide range of gears up to a diameter of 500 mm to be manufactured with cleanly, reproducible results.
|
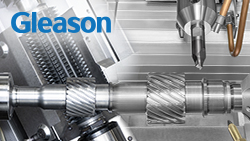 |
Horizontal Hobbing and Cutting Chamfering Machine |
The 100HCD Hobbing and Chamfering Machine is enhanced with a CNC chamfering/deburring station which works completely in parallel to the actual gear cutting process: productivity is not compromised by the chamfering process. Radial Chamfering allows for universal chamfering of gears – and even geared shafts with interfering contours – at comparatively low tool costs.
|
|
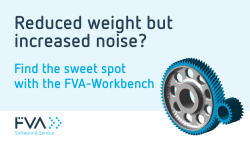 |
Dynamic simulation tools for optimized gear designs |
Tired of sacrificing noise for weight savings? The FVA-Workbench helps you design gears that are light and quiet. Simulate real-world behavior and detect excitation sources early with dynamic analysis and CAD-based modeling, no external FEM tools needed. Optimize weight and performance in one workflow. Find your gear design sweet spot.
|
|
|
|